
LUBE OIL BLENDING PLANT
WHAT IS LUBE OIL BLENDING PLANT?
A Lube Oil Blending Plant is a specialized facility where various lubricating oils are produced through the blending and mixing of base oils with additives. These plants are equipped with machinery and equipment designed to precisely control the blending process to achieve the desired specifications and performance characteristics of the final lubricant products. Capacity of Plant ranges from 5 MT per Day to 300 MT per Day Lube Oil Blending Plant.
There are two primary raw materials utilized in the manufacturing of lubricants:
• Base oil stocks for lubricants
• Additives
The process of blending and mixing base oil with additives results in the production of the final finished lubricating oil. Lubricating oil, a derivative of petroleum serves to mitigate friction between moving components within machines and engines. Its unique properties aid in reducing overheating, scuffing, rubbing, and corrosion. Consequently, lubricants contribute to prolonging equipment lifespan, optimizing the utilization of valuable resources, enhancing fuel efficiency, and ultimately mitigating greenhouse gas emissions.
LUBE BASE STOCK: One of the primary products derived from this process is base stock, which serves as the foundation for base oil. Base oil, utilized as a lubricant in machinery, requires the addition of specific chemicals known as additives to enhance its lubricating properties. These additives collectively serve various functions, with each additive serving a specific purpose, ultimately imparting distinct characteristics to the lubricant. The ratio of base oil to additives varies depending on the intended application, ranging from 85:15 to 90:10.
BASE OILS: Base oil, derived from highly refined crude oil or synthetic compositions, comprises approximately one percent of the total output of petroleum products from crude oil. It is a by-product obtained during the crude oil refining process, typically extracted alongside heavier fractions. Various operating conditions, such as moisture, dust, exposure to air, temperature fluctuations, pressure, corrosion, etc., influence the selection of base oil and additives required.
TYPES OF BASE OILS:
- Group 1
- Group 2
- Group 3
- Gas-to-liquids (GTL)
- SN500
- SN 150
- SN 70
- Bright stock (BS)

-
Automatic Batch Blending (ABB)
-
Inline Blending System (ILB)
-
Simultaneous Metered Blending Unit (SMB)
-
Skid-Mounted Lubricant Blending Plant
-
Pigging Unit
-
Ultrasonic Blending Technology
-
Viscosity Index Improver
-
Drum Decanting Unit (DDU)
-
IBC Decanting Machine (IBC)
-
Blending Kettle
-
Filling Machine Packaging Process
-
Automation
-
Laboratory Equipment
LUBE OIL BLENDING PLANT PROCESS:
01.
BLENDING SYSTEMS
02.
VISCOSITY INDEX IMPROVER
03.
DECANTING UNITS
04.
LABORATORY EQUIPMENTS
01. LUBE OIL BLENDING SYSTEMS
Automatic Batch Blending (ABB)
Advanced automation system featuring Smart Blend Software, DDU (Dilution Dispensing Unit), transfer pumps, TFH (Thermic Fluid Heater), filters, laboratory setup, and professional installation services. Implementing computerised technology has revolutionised lubricant blending processes, ensuring consistent product quality, minimising re-blending and laboratory costs, and maximising blend vessel utilisation.
One of the primary advantages of automatic batch blending is its ability to achieve precision mixing. Automated systems employ advanced technologies to accurately measure and control the quantities of each ingredient, ensuring that the blending process adheres meticulously to predefined formulations. This precision is crucial in industries where product specifications and quality standards are paramount.
Consistency is another crucial characteristic of automatic batch blending. These automated systems consistently deliver uniform results across multiple batches by following meticulously programmed recipes and predefined parameters. This consistency is critical to maintaining high product quality and meeting stringent industry standards. It also contributes to the reliability and predictability of the manufacturing process.
Efficiency is a fundamental aspect of automatic batch blending. Automation significantly streamlines the blending process, reducing the reliance on manual intervention. This not only minimizes the risk of human errors but also optimizes the utilization of resources, leading to increased overall efficiency in production. The streamlined and automated nature of the process contributes to faster production cycles and improved throughput, ultimately leading to significant cost savings.
BENEFITS OF AUTOMATIC BATCH BLENDING SYSTEM:
1. Enhanced Product Quality: Utilising computerised technology ensures consistent product quality.
2. Compliance: ABB facilitates ISO 9002 and ISO 14000 compliance.
3. Optimum Production: The system optimises production quality with excellent dosing accuracy and repeatability.
4. Process Flexibility: ABB enables meeting just-in-time requirements and offers process flexibility.
5. Waste Minimisation: ABB helps minimise waste generation, reducing environmental impact.
6. Lower Maintenance Costs: The system lowers maintenance expenses and is designed specifically for unit requirements.
7. Improved Profitability: ABB enhances plant profitability through efficient operations.
8. Reduced Manpower Costs: Semi-skilled labour can efficiently run the plant, lowering workforce expenses.
9. No Re-blending: ABB eliminates the need for re-blending, saving time and resources.
10. Accurate Management Budgeting: The system allows for accurate planning of grades and production volumes before real-time processing.
In conclusion, automatic batch blending represents a technological leap forward in the manufacturing landscape. It has become an integral and preferred method for industries that prioritise precision, consistency, efficiency, flexibility, traceability, and reduced wastage in their production processes. The adoption of automated batch blending systems underscores a commitment to delivering high-quality products in a reliable and sustainable manner, while also reaping the numerous benefits it offers.

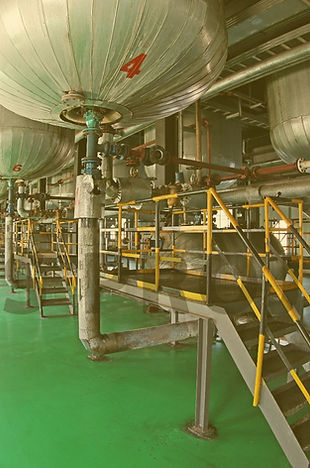


INLINE BLENDING SYSTEM (ILB)
ILB (Inline Blending System) lube oil blending plant machines is fully automatic with continuous blender and auto-cleaning system. The system uses a group of VFD (Variable Frequency Drive) controlled pumps, flow meters and automated valves. The entire process is automated and PLC controlled with SCADA interface Inline Blending System can be operated by smart phone or built-in touch screen with wi-fi connected to computer system. The whole process of ILB (Inline Blending System) is accurate and very easy to operate.
ILB (Inline Blending System) is composed of several dosing modules they are used for blending large batches that require consistent quality ILB is connected to input and output lines, where input line are connected with raw material storage tanks that is base oil & additives and output lines are connected with lube oil storage tanks or filling areas. ILB mixing technology eliminates the need for bulk storage tanks and speeds up the rate of production, reducing capital cost and making consistent quality of finished products, easy to pack and ready to be shipped.
Advantages of Inline Blending System
1. Large Blending Volumes.
2. Consistent quality
3. Minimum contamination occurs
4. Operated by smart phone or built-in touch screen
5. Quick turnover and less time consuming.
6. Blends have the option to be directly dispatched to the packing or shipping area.
SIMULTANEOUS METERED BLENDING ( SMB)
Simultaneous Metered Blending unit (SMB) are a turnkey blending system it’s much more advanced system of processing lubricants manufacturing plants It’s a combination of high volume production capacity of In Line Blending units (ILB) with operating flexibility of Automatic Batch Blending (ABB) Instead of blending in a kettle Components are simultaneously dosed into a header before discharging to tank for final mixing. SMB systems are engineered to concurrently gauge liquids using a Coriolis flow meter and ensure their precise proportional mixture via a central conduit. These Simultaneous Metered Blenders are compact modular setups that employ Micro Motion technology for accurate measurement and control. They function by accurately dispensing the appropriate proportions of various components into the central conduit, which then directs the blended mixture for subsequent homogenization.
Precision mixing is the hallmark of simultaneous metered blending. Every ingredient undergoes meticulous measurement according to predefined specifications. This commitment to precision guarantees not only accurate metering but also a consistently high-quality final product. This precision is maintained throughout the entire blending process, ensuring that each batch meets stringent quality standards.
In conclusion, simultaneous metered blending is not merely a technique; it is a transformative force in modern manufacturing. With its multifaceted advantages and widespread applications, this innovative method is steering industries towards a future characterized by efficiency, precision, and adaptability. The adoption of simultaneous metered blending underscores a commitment to excellence in manufacturing practices and a pursuit of optimal production outcomes.


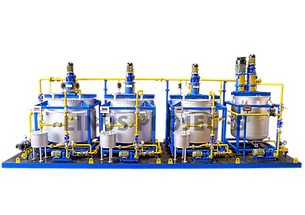.png)
Skid Mounted Lubricant Blending Plant
The Skid Based Lube Oil Blending Plant stands as a pinnacle of efficiency and innovation in the lubricant manufacturing industry. This state-of-the-art solution is meticulously designed to streamline the process of blending lube oils with precision and reliability. Mounted on a compact and modular skid, this plant offers a turnkey solution that optimizes space utilization, making it an ideal choice for industries where real estate is a critical consideration.
One of the key features of the skid-mounted lube oil blending plant is its versatility. The system accommodates a wide range of base oils and additives, allowing for the formulation of a diverse array of lubricant products tailored to specific industry needs. The modular design ensures flexibility in production, enabling manufacturers to adapt quickly to changing market demands and product specifications.
Equipped with advanced automation, the skid-mounted blending plant minimizes the need for manual intervention. Intelligent sensors, programmable logic controllers (PLCs), and user-friendly interfaces collaborate seamlessly to orchestrate the blending process with precision. This not only enhances the overall efficiency of the manufacturing process but also contributes to the production of consistently high-quality lubricants.
Whether deployed in the automotive, industrial, or aviation lubricant sectors, the skid based lube oil blending plant offers a comprehensive solution for manufacturers seeking efficiency, flexibility, and reliability in their lubricant production processes. As a testament to technological advancements in the industry, this plant stands as a strategic investment, empowering manufacturers to meet market demands, maintain product quality, and stay at the forefront of the dynamic lubricant market.
PIGGING UNIT FOR CONTAMINATION REDUCTION
Pigged pipeline technology proves advantageous for the transfer of a diverse range of products. Pigged manifolds seamlessly interconnect numerous source tanks with various destinations like filling and loading.
Addressing a significant challenge in Lube Oil Blending Plants, pigged manifolds seamlessly interconnect numerous source tanks with various destinations like filling and loading. This innovative approach enhances efficiency and resolves complexities associated with managing multiple product transfers within the blending facility.
Pigging units serve the purpose of cleaning residual products from pipelines to prevent contamination, and they are strategically engineered to minimize the number of pipelines within a plant. The key elements of a pigging unit include the launcher, receiver, and catcher positioned at opposite ends of the pipe. A valve is incorporated to regulate the compressed air or gas utilized for propelling the pig, which travels through the pipeline to eliminate any remaining liquid. The pig can be easily inserted into or extracted from the catcher for maintenance purposes.
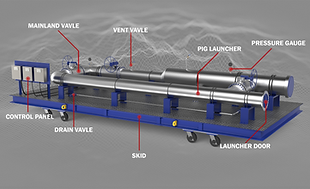

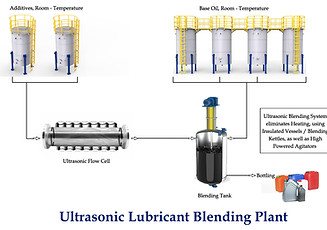

Ultrasonic Technology Lube Oil Blending Plant
A groundbreaking process for blending lubricants utilizing ultrasound technology has been established. This approach does away with the need to heat base oils and additives, which is a notable shift from standard practices. The technology behind ultrasonic processors harnesses high-frequency sound waves to create acoustic cavitation, where small bubbles form, expand, and collapse within a liquid medium. This process effectively converts electrical energy into mechanical vibrations, known as ultrasound. This method incorporates an ultrasonic flow cell to blend the oil components effectively, yielding a lubricant that is uniformly mixed.
The ultrasonic tubular processor is designed with a 4-inch diameter and is made from stainless steel pipe. This robust design includes piezo-crystals that are fundamental to its function. The piezo-crystals create a piezo-electric effect. When powered, they collaborate with transducers to transform electrical energy into ultrasound energy.
Ultrasonic waves generate intense cavitation, which aids in the even distribution of molecules. This procedure is vital for achieving a uniform and superior blend of oils. Ultrasonic blending provides various benefits, including better energy efficiency and reduced processing times compared to standard techniques. The elimination of heating requirements simplifies the process and cuts down energy consumption, leading to a significant reduction in carbon emissions.
In larger applications, it is feasible to link several ultrasonic flow cells in a cascade arrangement. This method delivers two significant benefits: improved energy efficiency and enhanced process speed. The system not only expedites operations but also conserves resources and cuts costs, where sustainability and efficiency are crucial. This technique corresponds with the increasing need for environmentally sustainable practices in manufacturing.
Advantages Ultrasonic Lubricant Oil Blending Machinery
-
The compact design reduces the need for space.
-
Operations does not require heating.
-
Energy consumption is lower than that of conventional methods, such as heating and stirring techniques.
-
Ideal for blending in restricted spaces.
-
Ultrasonic blending is more energy-efficient for smaller batches.
-
Ultrasonic waves improve the consistency and accuracy of blends.
-
Effective distribution of additives, including nanoparticles, enhances lubrication.
-
Flexible ultrasonic systems can handle a variety of base oils and additives.
-
Environmentally sustainable production is achieved through decreased energy usage and waste reduction, significantly lowering carbon emissions.
02. VISCOSITY INDEX IMPROVER MFG.
Viscosity Index Improver Mfg. Plant
Viscosity Index Improver Manufacturing Plant, designed to revolutionize the production process of viscosity index improvers. Built with innovation and efficiency in mind, our modular plant offers unparalleled flexibility, scalability, and performance, meeting the dynamic demands of the lubricant industry. This is use in Lubricant Blending Plant.
It"s equipped with advanced process automation and control systems, leveraging cutting-edge technology to optimize production efficiency and product quality. From raw material handling to final product packaging, every step of the manufacturing process is meticulously monitored and controlled to ensure consistency and reliability. with a focus on sustainability, our modular plant incorporates energy-efficient technologies and waste minimization strategies, minimizing environmental impact while maximizing resource utilization. Additionally, our plant adheres to stringent quality standards and regulatory requirements, ensuring that every batch of viscosity index improver meets the highest quality specifications.
The Viscosity Index Improver Kettle is a specialized equipment used in the manufacturing process of viscosity index improvers for lubricants. It is designed to precisely control and optimize the viscosity index of lubricant formulations, ensuring they meet specific performance requirements.
Overall, the viscosity index improver kettle plays a critical role in the production of lubricants with optimal viscosity characteristics, contributing to the performance and longevity of machinery and equipment in various industries.

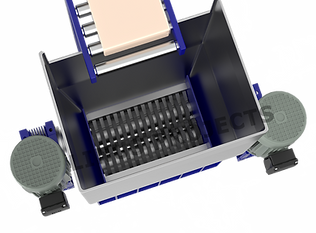
03. DECANTING UNITS
DRUM DECANTING UNIT (DDU) FOR LUBRICANT ADDITIVES
Drum Decanting Unit (DDU) represents a mechanized and automated solution for introducing small-volume additives into blends. These units come equipped with conveyor belts, load cells, control systems, rinse tanks, and swivel lances. Drum Decanting Units contribute to heightened efficiency and safety. The DDU is meticulously engineered for pumping and precisely dosing highly viscous liquids from drums, seamlessly integrating them into formulation processes. This technology is particularly recommended for scenarios demanding the utmost accuracy in dosing and repeatability.
Drum Decanting Unit can be used for emptying a defined value of additives without any cross contamination into the production process of lubricants. The product has various operational features such as decanting operation, Rinsing operation, drum tilting, heating, etc. The high-performance DDU brings the expensive additive into the production process without neither product loss, waste oil onset, and high-precision dosing by weighing technology. The unit is easy to handle, satisfies the highest safety standards, and runs in clean and completely closed conditions.
LINUS PROJECTS(INDIA) Drum Decanting Unit can be used for emptying a defined value of additives without any cross contamination into the production process of lubricants.
The product has various operational features such as decanting operation, Rinsing operation, drum tilting, heating, etc.
The high-performance DDU brings the expensive additive into the production process without neither product loss, waste oil onset, and high-precision dosing by weighing technology. The unit is easy to handle, satisfies the highest safety standards, and runs in clean and completely closed conditions.
Operation of DDU:
A typical DDU uses roller conveyors to feed and discharge the drums or totes - one at a time - onto the drum-weighing platform.
-
The proper drum is selected and fed into the platform in sequence by the operator.
-
The platform is mounted on compression load cells that weigh the amount of each material, and a tilting device is included to ensure maximum product recovery and removal.
-
Additionally, a suction telescopic nozzle, equipped with a flexible hose, is inserted into the drum to withdraw the liquid.
-
A screw Pump is provided to suck the oil and transfer it to the dosing or blending system.
-
The operator initiates production using the supervisory Control System which pulls and verifies the component recipe and line up.
-
When the set amount of material has been withdrawn from each drum, the lance is removed, cleaned in a rinsing tube and restored for the next drum in sequence.
-
A rinse tank equipped with a heating system is included.
-
The system flushes the nozzle and drum to remove any remaining material, ensuring maximum product recovery and minimising waste or cross-contamination.
-
Additionally, each empty drum is rinsed with a low viscosity component to minimise any residual material in the drum or tote.
-
A separate hose with a quick-release coupling is provided to add the finishing oil from any system at a particular time.
Advantages of our Drum Decanting Unit:
-
Exact, reliable, and reproducible dosing of additives in the production process
-
Saving additives by emptying the drums.
-
No waste oil in the production process
-
No cross-contamination by cleaning the drum with hot rinse oil.
FEATURES AND BENEFITS OF OUR DDU
-
Eliminate manual dosing, cleaning, and overtreating for safer, efficient operations with the fully automated system, including Clean-In-Place technologies
-
Maximise product recovery and removal with tilting devices to empty drums.
-
Increase flexibility by accommodating additives with a wide viscosity range or by manually adding components as required by the recipe.
-
Avoid over-treating through accurate dosing
-
measures setto computention of the decanting operation.
-
Directly blend components packaged in drums or totes.
-
Reduce footprint with a newly enhanced, more compact unit.
-
Increase operational efficiency by selecting up to 9 different control phases based on recipe requirements
-
No contamination of the rinse tank by lance cleaning.





IBC DECANTING MACHINE (IBC)
Intermediate Bulk Container Tank Decanting Machine is a specialized piece of equipment engineered to efficiently and safely transfer liquids from IBC tanks. Designed to meet the rigorous demands of various industries, this decanting machine is indispensable in sectors such as lubricants, grease, chemical manufacturing, food and beverage processing, pharmaceuticals, and any application where bulk liquid handling is necessary.
IBC decanting machine offers both pneumatic and hydraulic options, providing flexibility and reliability in its operation. At the heart of the system is a vertically mounted screw pump, capable of transferring liquids at a rate of up to 2000 liters per hour (LPH). This robust pump system is available with power capacities ranging from 1HP to 5HP, ensuring it can handle a wide range of liquid viscosities and transfer needs. Equipped with advanced Programmable Logic Controllers (PLC) and Human Machine Interface (HMI) options, allowing for enhanced control, automation, and ease of use based on specific requirements.
04. LABORATORY EQUIPMENT
LABORATORY EQUIPMENT FOR TESTING
Laboratory testing for conducting quality assessments.
Lubricant Oil serves as the essential fluid for machinery, and analyzing oil samples is crucial for evaluating the operational condition and efficiency of the equipment. Regular oil testing offers multiple advantages: it extends the lifespan of the machinery, optimizes oil change schedules, and provides insights into the dynamic conditions within the equipment. This information is vital for planning maintenance activities accurately, thereby reducing the likelihood of unexpected breakdowns and minimizing the risk of severe failures.
After every batch of Lubricant Oil is Blended, its sample are taken to Laboratory for checking its Viscosity Index. Too high viscosity can impede flow, while excessively low viscosity may compromise parts protection.
Below Mentioned are critical equipment used in the Lubricant plant
-
VISCOSITY BATH SUITABLE TO 100 °C & 40°C
-
FLASHPOINT APPARATUS COC
-
POUR POINT 1 CHAMBER AT 51 C
-
HYDROMETER M-50 2 NOS
-
THERMOMETER-IP 51
-
TBN TITRATION APPARATUS
-
MUFFLE FURNACE
-
LAB ANALYTIC SCALE
-
LAB CHEMICALS FOR TBN
-
GLASS APPARATUS FOR LABORATORY
-
CONE PENETROMETER
-
AUTOMATIC GREASE WORKER
-
WHEEL BEARING TEST

.jpeg)
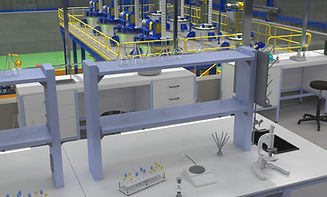
LUBE OIL BLENDING PLANTS - SECTION:
01.
BLENDING
02.
FILLING LINE
03.
UTILITY
04.
AUTOMATION
01. BLENDING SECTION
LUBE OIL BLENDING KETTLE
A lubricant oil blender is a specialized industrial machine used in a Lube Oil Blending Plant to precisely mix base oils and additives to create various lubricant formulations. A lubricant oil blender typically consists of a robust framework or chassis that supports its components and machinery. At the center of the blender is the blending vessel or tank, which serves as the primary container for the blending process. This vessel is designed to hold significant volumes of base oils and additives and is equipped with mixing mechanisms to ensure thorough blending and uniform distribution of ingredients. Capacity ranges from 1 MT to 20 MT Blenders.
The blending vessel is constructed from either Mild Steel or Stainless Steel IS 2062 material and features an open top design with a partially dished bottom. A hinged top lid is provided for easy access to the main blender. At the bottom, a ball valve is installed for discharge purposes, along with a sample valve for quality control. Surrounding the main blender is an MS jacket, complete with inlet, outlet, drain, and vent fittings. Additionally, each vessel is equipped with a temperature probe and fittings to ensure precise temperature control.
Our blenders are meticulously engineered to comply with ASME standards and are capable of producing various grades of lubricants, including engine oil, gear oil, hydraulic oil, special-purpose oil, marine oil, and viscosity improvers. To facilitate precise dosing of additives, each blender is equipped with an additive dosing bunker.
The output shaft of the gearbox is connected to a stool housing, which includes bearings, oil seals, and gland packings to ensure smooth operation. The blending vessel is designed to withstand temperatures of up to 200˚C and is insulated with rock wool and clad with GI sheets for enhanced thermal efficiency and durability.
FEATURES:
1. Precision Mixing: Lubricant oil blenders are engineered with precise mixing mechanisms, ensuring consistent blending to achieve the desired composition and quality of lubricant formulations.
2. Versatility: These blenders are adaptable to a wide range of base oils, additives, and lubricant formulations, allowing for flexibility in production to meet diverse industry requirements.
3. Customization: Many lubricant oil blenders offer customizable blending parameters, enabling operators to adjust mixing speeds, agitation levels, and other settings to optimize blending performance and meet specific product specifications.
4. Automated Controls: Advanced lubricant oil blenders feature automated control systems that monitor and regulate blending parameters such as mixing speed, temperature, and ingredient ratios, ensuring accurate and repeatable blending results.
5. Easy Maintenance: Lubricant oil blenders are designed for straightforward maintenance, with accessible components and features that facilitate routine upkeep tasks to minimize downtime and sustain optimal performance.
6. Safety Measures: These blenders incorporate safety features such as emergency stop buttons, safety interlocks, and protective guards to ensure operator safety during operation.
7. Hygienic Design: Constructed from sanitary materials and compliant with stringent hygiene standards, lubricant oil blenders prevent contamination and maintain the purity of the lubricant products.
8. Scalability: Lubricant oil blenders are scalable to accommodate varying production capacities, from small-scale operations to large-scale manufacturing facilities, ensuring suitability for different production demands.
Overall, lubricant oil blenders play a pivotal role in the lubricant manufacturing process, providing precise blending capabilities, flexibility, and advanced features to produce high-quality lubricants for diverse applications in industries worldwide.

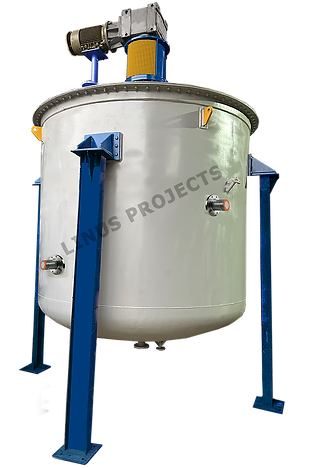


BASE OIL & RECIRCULATION PUMP
Gear pumps are essential components utilized for transferring various types of base oils from the tank farm to ABB blenders within lubricant grease projects. The base oils, including SN900, SN150, SN100, SN250, among others, are crucial raw materials for the blending process. These pumps function by utilizing the meshing of gears to displace fluid, making them a prevalent choice for hydraulic fluid power applications. Gear pumps play a pivotal role in the seamless operation of lubricant grease projects, ensuring the efficient and precise transfer of base oils to the blending units. Their reliability, versatility, and effectiveness make them indispensable assets in the lubricant manufacturing industry, facilitating the production of high-quality lubricants for various industrial applications.
FEATURES:
1. Versatility
2. Efficient Displacement
3. Robust Construction
4. Precise Control
5. Compact Design
6. Compatibility
ADDITIVE DOSING PORT
An additive dosing tank in a lube oil blending setup is a specialized vessel integral to the manufacturing process of lubricants. In the context of a lube oil blending tank, an additive dosing tank is a crucial component designed to precisely measure and introduce additives into base oils during the blending process. Constructed from durable materials like stainless steel or Miled Steel, these tanks are engineered to withstand the chemical properties of various additives and ensure the integrity of the lubricant formulation.
The additive dosing tank is strategically positioned within the lube oil blending setup, typically adjacent to or integrated with the main blending vessel. It features dedicated inlet ports or connections through which both base oils and additives are introduced into the tank.
Internally, the additive dosing tank is equipped with mixing mechanisms such as agitators or stirrers, powered by motors or pneumatic systems. These mechanisms ensure thorough blending and homogenization of the base oils and additives, facilitating the creation of a uniform lubricant formulation.


FINISHED PRODUCT TANK
A Finished Product Tank is an essential component in the lubricant manufacturing process, serving as the storage vessel for the final blended lubricant products before they are packaged and distributed. A finished product tank is a large, cylindrical container typically constructed from stainless steel or other durable materials to ensure compatibility with a wide range of lubricant formulations. These tanks are designed to hold significant volumes of finished lubricant products and are often equipped with features to maintain the quality and integrity of the stored lubricants.
The tank is typically located within the lubricant manufacturing facility, either adjacent to the blending area or in a dedicated storage area. It is connected to the blending equipment through piping or conveyance systems, allowing for the direct transfer of finished lubricants from the blending vessels to the storage tank.
Finished product tanks are equipped with inlet and outlet ports that facilitate the filling and dispensing of lubricants. These ports may be fitted with valves or other control mechanisms to regulate the flow of lubricants in and out of the tank.
BASKET FILTERS
In a lube oil blending plant, basket filters play a crucial role in ensuring the quality and purity of the lubricant products. These filters are strategically incorporated into the processing line to remove impurities, contaminants, and solid particles from the base oils and additives before they are blended together.
The basket filters typically consist of a cylindrical housing with a perforated or mesh-lined basket inside, serving as the filter element. As the base oils and additives pass through the filter housing, any particulate matter larger than the filter's mesh size is trapped inside the basket, while the clean liquid flows through. This filtration process helps to eliminate debris, dirt, and other unwanted substances that could compromise the performance and longevity of the lubricant products.
Basket filters are particularly essential in lube oil blending plants where precise control over the quality and composition of the lubricants is paramount. They ensure that the final blended lubricant formulations meet the required standards and specifications for various industrial applications. Additionally, basket filters are designed to handle the high flow rates typically encountered in lube oil blending operations without causing significant pressure drops or disruptions to the production process. Their efficiency, reliability, and ease of maintenance make them indispensable components in the quest for producing high-quality lubricants in lube oil blending plants.



LOAD CELLS
Load cells serve as critical components for precisely measuring the weight of ingredients during the blending process. These specialized sensors are integrated into the blending equipment to ensure accurate and consistent formulation of lubricant products. Load cells are typically installed beneath the blending vessels or tanks where the base oils, additives, and other ingredients are mixed. As the ingredients are dispensed into the blending vessel, the load cells detect and measure the weight of each component in real-time.
This information is then relayed to the control system of the blending plant, allowing operators to monitor and adjust the ingredient ratios as necessary to achieve the desired lubricant formulations. Load cells are calibrated to withstand the harsh operating conditions within the blending plant, including variations in temperature, pressure, and vibration. They provide precise measurements with high levels of accuracy, ensuring that the final lubricant products meet the required specifications and quality standards. Additionally, load cells offer advantages such as rapid response times, minimal maintenance requirements, and compatibility with various blending processes. Overall, load cells play a crucial role in optimizing the efficiency, consistency, and quality of lubricant production in blending plants by enabling precise control over ingredient dosing and formulation.
Load cells offer several advantages:
1. Built-in Safety: They provide inherent safety measures against vessel tilting and build forces, ensuring stability during operations.
2. Thermal Flexibility: Load cells accommodate vessels' expansion and contraction caused by thermal effects, maintaining accurate measurements despite temperature fluctuations.
3. Copper Earthing Strip: Equipped with a flexible copper earthing strip, load cells are safeguarded against lightning strikes or welding currents, enhancing their durability and reliability.
4. Cable Protection: They feature built-in load cell cable protection plates and overload protection plates, along with heat insulation pads, to shield against external damage and ensure uninterrupted performance.
PLATFORM / STRUCTURE
The platform or structure of a lube oil blending plant is meticulously engineered to provide a robust foundation and support system for intricate blending operations. Constructed from durable materials such as steel or concrete, it is designed to withstand the rigors of industrial environments and ensure the safety and stability of the entire facility. The platform's layout is carefully planned to optimize workflow and accommodate various components and equipment essential for the blending process.
At its core, the platform serves as a sturdy base for housing blending vessels, which are the heart of the operation. These vessels are securely positioned on the platform, allowing for efficient mixing of base oils, additives, and other ingredients to create high-quality lubricant formulations. Additionally, the platform supports the installation of mixing equipment, such as agitators or stirrers, which are instrumental in achieving uniform blending and consistency in the final product.
In addition to the blending vessels and mixing equipment, the platform accommodates piping systems that transport raw materials and finished products throughout the facility. This includes pipelines for delivering base oils and additives to the blending vessels, as well as conduits for transferring blended lubricants to storage tanks or packaging lines. Moreover, the platform may incorporate elevated platforms or walkways, providing convenient access to equipment for maintenance, inspection, and monitoring purposes. These elevated structures enhance operational efficiency and ensure the safety of personnel working within the facility.
Importantly, the platform is engineered to mitigate the effects of heavy machinery and equipment vibrations, as well as dynamic loads associated with blending operations. This ensures the structural integrity of the facility and minimizes the risk of equipment damage or malfunction. Overall, the platform serves as a critical infrastructure element in the lube oil blending plant, facilitating efficient, safe, and reliable production processes. Its robust construction, strategic layout, and adherence to safety standards contribute to the smooth operation and longevity of the blending facility.
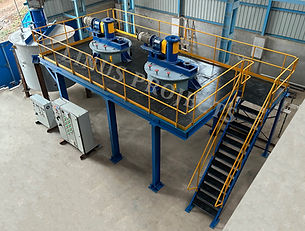

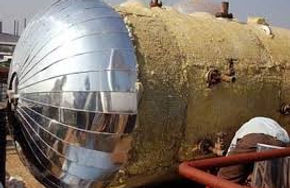
INSULATION FOR BLENDING TANKS
Insulation of blenders helps in maintaining optimal operating conditions and enhances efficiency in the blending process. Here's a description of the insulation typically used for blenders:
Blender insulation is designed to minimize heat loss and maintain consistent temperatures within the blending vessel during the mixing process. This insulation is applied to the exterior surface of the blender's main body and jacket, providing a thermal barrier that prevents heat from escaping or entering the vessel.
The insulation material is often composed of high-quality materials such as rock wool, fiberglass, or mineral wool, known for their excellent thermal insulating properties. These materials are chosen for their ability to withstand high temperatures and resist degradation over time, ensuring long-lasting performance in demanding industrial environments.
The insulation is carefully applied to the blender's exterior using a combination of techniques such as wrapping, spraying, or cladding, depending on the specific design and requirements of the blender. It is custom-fitted to the shape and size of the blender, ensuring complete coverage and effective thermal protection.
Overall, insulation for blenders plays a crucial role in optimizing energy efficiency, reducing heat loss, and maintaining precise temperature control during lube oil blending operations.
02. FILLING SECTION
FILLING MACHINE
In a lubricant oil blending plant, filling machines play an important role in the packaging process, ensuring efficient and accurate filling of lubricant products into containers of various sizes. These machines are designed to handle the specific requirements of lube oil blending operations and are tailored to meet the demands of high-volume production.
The filling machine of Linus Projects used in lube oil blending plants is a precision-engineered piece of equipment designed to fill containers with lubricant products with precision and consistency. It typically consists of a conveyor system that transports empty containers to the filling station, where they are filled with the desired amount of lubricant oil.
The filling machine is equipped with multiple filling heads to increase throughput and efficiency, allowing for the simultaneous filling of multiple containers. These filling heads are designed to accommodate different container sizes and shapes, ensuring versatility and flexibility in production. Depending on the specific requirements of the blending plant, the filling machine may operate in either automatic or semi-automatic mode.
In automatic mode, the filling process is fully automated, with containers being filled, capped, and labeled without the need for manual intervention.
In semi-automatic mode, operators oversee the filling process and manually control certain aspects of the operation.
Filling Range : 500 ml to 5 liters
No of Filling Heads : 2 to 14 Head
Filling Mode : Automatic / Semi Automatic
Application : Lubricant Oil
FEATURES:
1. High-Speed Operation
2. Versatility
3. Precision Filling
4. Automated Operation
5. Programmable Controls
6. Safety Features
7. Easy Maintenance
8. Robust Construction


BARREL FILLING MACHINE
The Barrel Filling machine in a lube oil blending plant is a critical piece of equipment designed to efficiently and accurately fill barrels with lubricant products. This machine plays a vital role in the packaging process, ensuring that each barrel is filled to the correct level with the precise amount of lubricant required. It operates seamlessly within the production line, contributing to the overall efficiency and effectiveness of the plant's operations.
Utilizing advanced technology and precise mechanisms, the barrel filling machine precisely dispenses lubricant into each barrel, minimizing wastage and ensuring consistent product quality. Its automated operation streamlines the filling process, allowing for high throughput and minimizing downtime.
Equipped with intuitive controls and monitoring systems, the barrel filling machine offers operators the ability to adjust filling parameters and monitor production in real-time. This ensures accurate filling levels and enables quick adjustments to accommodate different barrel sizes or product specifications.
Additionally, the barrel filling machine is designed with safety features to prevent spills, leaks, and other potential hazards during the filling process. Robust construction and durable materials ensure reliability and longevity, even under heavy-duty usage in industrial settings.
Our Drum filling machine is suitable to fill the 25 Ltr's as well the machine is fully adjustable.
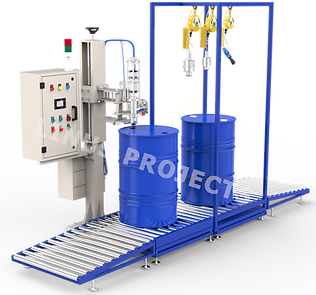


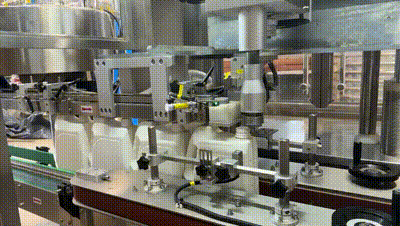
CAPPING MACHINE
The capping machine stands as a pivotal element within the lube oil blending plant, serving as the linchpin of the packaging process. Its primary function revolves around the secure sealing of containers that have been meticulously filled with lubricant products. As the final step before distribution, the capping machine ensures that each can is tightly sealed, safeguarding the integrity of the product within.
Our capping machine comprises of Cap Vibrator for cap orientation & capping unit. The caps fed in the vibratory hopper are properly oriented here. The properly oriented caps are brought out through chute and supported at the end by spring-loaded fingers the containers as it comes out of the filling station move to the capping unit, where-in it picks up the cap and goes towards the capping head. The caps are subsequently tightened through a magnetic clutch system. The capped bottles finally emerge out of the machine through a discharge conveyor.
With meticulous precision, the capping machine meticulously applies caps onto the filled cans, guaranteeing a snug fit that prevents any leakage or spillage during handling and transportation. This process is executed with utmost accuracy, ensuring that each cap is affixed uniformly and securely onto every can. the capping machine is designed to accommodate various types and sizes of caps commonly utilized within the industry. Whether it's screw caps, snap caps, or press-on caps, the capping machine seamlessly adapts to the specific requirements of the packaging, ensuring compatibility with diverse packaging needs.
FEATURES:
1. Versatility
2. High-Speed Operation
3. Precision Capping
4. Adjustable Torque
5. Automated Operation
6. Integrated Controls
INDUCTION SEALING MACHINE
The induction sealing machine in a lube oil blending plant is an essential component of the packaging process, responsible for securely sealing containers filled with lubricant products.
Nestled within the lube oil blending plant, the induction sealing machine serves as a critical safeguard in the final stages of packaging, ensuring that each container is hermetically sealed to preserve the integrity of the lubricant products within. Its operation seamlessly integrates into the packaging line, providing a reliable and efficient means of applying tamper-evident seals to containers.
Utilizing advanced induction heating technology, the sealing machine creates a strong and airtight seal between the container and its closure, effectively preventing tampering, leakage, and contamination. As containers pass through the machine, an electromagnetic field is generated, causing the foil liner on the closure to heat and bond with the container's rim, forming a secure seal.
The induction sealing machine operates with precision and speed, keeping pace with the high-volume production rates within the lube oil blending plant. Its efficient performance ensures seamless integration into the packaging line, contributing to overall productivity and throughput.
Equipped with intuitive controls and user-friendly interfaces, the sealing machine offers ease of operation, allowing operators to adjust sealing parameters and monitor the process with accuracy. This ensures consistent and reliable sealing performance, meeting stringent quality standards and regulatory requirements.
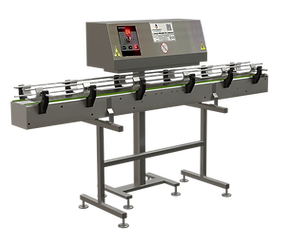



INK JET / LASER PRINTER
Automatic solution for printing batch identification codes, MRP, best before and packaged dates, plus QR codes onto almost any material, including specialist applications such as food and metals. CIJ coding & marking machines offer high-speed, reliable batch, lot, MRP & date coding for product identification and traceability. Our continuous ink jet batch printing machines can code onto a wide range of materials, even in dusty, hot, and wet environments
The inkjet printer is responsible for imprinting essential information such as batch numbers, expiration dates, and product codes onto the containers filled with lubricant products.
At the heart of the lube oil blending plant, the inkjet printer stands as a key player in the final stages of production, ensuring that each container leaving the facility is appropriately labeled with critical information. As the containers move along the packaging line, the inkjet printer seamlessly integrates into the process, providing a swift and efficient means of marking essential details onto the packaging.
Utilizing advanced inkjet printing technology, the printer precisely deposits ink onto the surface of the containers, creating clear and legible markings that withstand handling and storage. This method offers unparalleled versatility, allowing for the customization of text, symbols, and graphics to meet specific labeling requirements.
LABELLING MACHINE
The labeling machine in a lube oil blending plant is a crucial component of the packaging process, responsible for applying informative and branding labels onto containers filled with lubricant products.
Situated within the bustling confines of the lube oil blending plant, the labeling machine stands as a pivotal player in the final stages of production, ensuring that each container leaving the facility is accurately and attractively labeled. As containers journey along the packaging line, the labeling machine seamlessly integrates into the process, providing a swift and efficient means of applying labels onto the packaging.
Employing advanced labeling technology, the machine precisely affixes labels onto containers with precision and accuracy, creating a professional and polished appearance. This method offers versatility, allowing for the application of various types of labels, including product information, branding, barcodes, and regulatory compliance labels.
Furthermore, the labeling machine is designed for reliability and durability, capable of withstanding the demanding conditions of industrial environments. Its robust construction and advanced technology ensure consistent performance, minimizing downtime and maximizing uptime to meet production deadlines effectively.

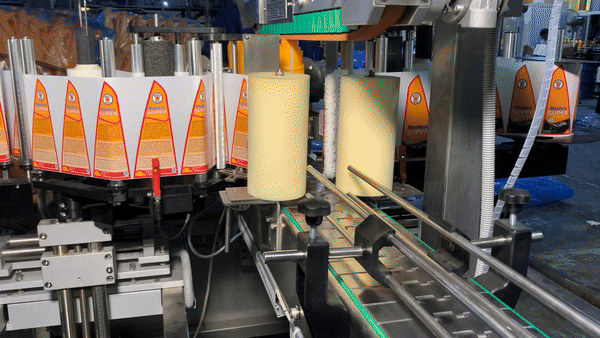


CARTON TAPING MACHINE
The Carton taping machine stands as an indispensable workhorse in the final stages of the packaging process. Tasked with the critical responsibility of securely sealing cartons filled with precious lubricant products, this machine executes its duty with precision and reliability.
As each carton makes its way through the production line, the carton taping machine springs into action, seamlessly and efficiently sealing the cartons to safeguard the integrity of the contents within. With deft precision, it applies adhesive tape along the seams of the cartons, ensuring a firm and durable seal that withstands the rigors of storage and transportation.
By adeptly sealing the cartons, the machine plays a vital role in preserving the quality and integrity of the lubricant products housed within. It shields them from potential damage, contamination, or tampering, ensuring that they reach their destination in pristine condition, ready to fulfill their intended purpose.
In essence, the carton taping machine serves as a silent guardian of product quality and customer satisfaction within the lube oil blending plant. Its steadfast operation and unwavering reliability underscore its indispensable role in the packaging process, making it an essential asset in the plant's arsenal of equipment.
Carton size in mm (L x W x H): 150 X 150 X 100 (Min) X 450 X 500 (Max)
Carton Weight : maximum 25 Kgs.
Speed - No. Of cartons / hr : 200 - 800
Machine bed height : 600 – 800 mm
Tape width : 48 mm. (2”)
Tape overlaps : 50 mm.
Tape Core diameter :75 mm.
Robotic Packaging
Technological progress in packaging design and functionality is witnessing significant growth, particularly in the automotive sector's lubricant packaging market. The rise of online sales for consumer lubricants is emerging as a notable trend in the retail industry, further driving the global expansion of Lubricant Robotic Packaging. Additionally, there is an increasing consumer awareness regarding environmental cleanliness and sustainable practices. Consequently, it is crucial for packaging to be developed with a focus on enhanced ease of cleaning, recycling capabilities, and reusability.
Robotic Process Automation (RPA) solutions, which include both rule-based robots and Intelligent Process Automation (IPA), have been instrumental in facilitating digital transformation across various organizations. In order to thrive in a competitive and rapidly evolving industrial environment, it is essential to remain informed about technological advancements and leverage them proactively to gain an edge over competitors. As the robotics sector expands, an increasing number of skilled professionals are entering the workforce.
Robotic Process Automation (RPA) Benefits:
-
Improved operational efficiency and reduced costs.
-
Increased precision and uniformity in processes.
-
Decreased likelihood of errors.
-
Accelerating the processing time, leading to higher productivity.
-
Flexible performance in challenging environments.

03. UTILITY


THERMIC BOILER
Linus Projects specializes in providing top-quality, fuel-efficient burners paired with boilers, catering to both steam and thermic fluid applications. The core heating unit comprises a robust double-jacketed external shell crafted from sturdy M.S. Sheets. It incorporates an Aluminum reflector, serving to preheat the combustion air while also offering efficient heat insulation.
The heart of the system features specially engineered multi-start, concentric helical coil assemblies constructed from B.S. 3059, Part I, 9 Gauge, Boiler Tubes. This design ensures prolonged operational life and exceptional performance, even in high-temperature environments.
For combustion, the setup integrates a pressure jet burner assembly from RIELLO ITALY, renowned for its reliability and efficiency. This burner assembly includes an integral oil pump and combustion blower assembly driven by a motor, facilitating seamless on/off control for optimal operational efficiency.
The Thermic boiler, also known as a thermal fluid heater or thermal oil heater, is a specialized type of industrial boiler designed to generate heat by heating a thermal fluid, typically a heat transfer oil. This fluid circulates through the boiler system, transferring heat to various components of the lube oil blending process, such as heating tanks, blending vessels, and reactors.
Constructed from high-quality materials such as stainless steel or carbon steel, the thermic boiler features a robust outer shell designed to withstand high temperatures and pressure. Inside the boiler, a series of heating coils or tubes are immersed in the thermal fluid, facilitating the transfer of heat from the combustion chamber to the fluid.
The boiler system is equipped with a burner unit responsible for combusting fuel, such as natural gas, diesel, or heavy oil, to generate heat. The combustion process heats the thermal fluid circulating within the boiler, raising its temperature to the desired level for the blending process.
FEATURES:
1. High Thermal Efficiency
2. Wide Temperature Range
3. Versatility
4. Compact Design
5. Advanced Control Systems
6. Environmental Considerations
DRUM TROLLEY
Drum Trolley is a specialized handling equipment designed to transport and maneuver drums safely and efficiently within industrial environments.
Drum holder: by means of fabricated belt & pipe with positive gripping.
Structure: simplex single mast structure made from heavy-duty ‘c’ channel section. It would be supported by heavy-duty deep grooved guide rollers. Forks lifting would be by means of 2nos. Duplex chain & design pulley.
Handle: designed for best maneuverability & made of M. S. Pipe.
Wheel: 8” x 2” nylon swivel castor wheel with 6204zz double ball bearing
Paint: auto-finish paint.
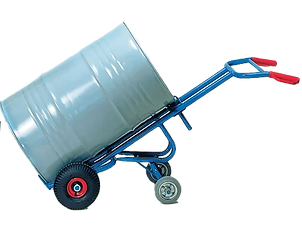

DRUM LIFTER & TILTER
Drum lifters and tilters play a vital role in the industrial sector, particularly in loading, unloading, and emptying drums used in various applications such as engineering and lubricant blending. These essential pieces of equipment are indispensable for efficiently handling drums, ensuring precise measurement and controlled pouring of contents into blenders or other processing equipment.
At the heart of a drum lifter and tilter is its robust construction, comprising a carriage assembly, hydraulic system, and hydraulic cylinder. The carriage assembly provides a stable platform for securely gripping and lifting drums, while the hydraulic system facilitates smooth and controlled lifting and tilting operations. The hydraulic cylinder is the powerhouse of the equipment, responsible for exerting the necessary force to lift and tilt heavy drums with ease.
Whether it's transferring lubricants for blending or handling other industrial materials, drum lifters and tilters are indispensable tools for maintaining operational efficiency and productivity. Their reliable performance, ergonomic design, and safety features make them essential equipment for any facility where drums are a common sight. With their ability to handle heavy loads with ease and precision, drum lifters and tilters are indispensable assets in modern industrial operations.
DRUM HEATING OVEN
The Drum Heating Oven is engineered to enhance the efficiency and ease of your industrial operations by offering a straightforward and dependable solution for heating and regulating the temperature of materials contained in drums or barrels. Whether dealing with oils, chemicals, resins, or other substances requiring accurate temperature management, this oven guarantees uniform and consistent heating, thereby alleviating the challenges associated with manual heating techniques or variable outcomes.
Drum heating ovens are constructed from robust materials designed to endure the demands of industrial applications. They also offer energy efficiency, allowing for a reduction in energy usage while ensuring peak performance. Additionally, equipped with safety features such as insulated doors and thermal shut-offs, these ovens provide a reliable and secure operational environment.
In short, a drum heating oven not only enhances time management but also guarantees that your materials are prepared for use precisely when required, thereby streamlining and optimizing your production process.
Manufacturing Many Types of Drum Heating Ovens.
-
Electric Cabinet Ovens for Drum & Barrel Heating Ovens.
-
Steam Drum Heating Oven.
-
Drum Spinning Heating Oven.
-
Temperature Control & Flameproof Sensors Drums Heating Oven.
-
Thermic Fluid Drum Heating Oven.


PALLET TRUCK
Manual Pallet Trucks Which Are Supplied In Rounds, Flats N Plates Sections. Hand Pallet Trucks Manual & Hydraulic Are Used to By Major Industrial Units Hand. Pallet Trucks Manual & Electric Is Being Supplied to The Consumers.
A pallet truck, also known as a pallet jack or pump truck, is a manual or electrically powered device used for lifting and moving palletized loads within warehouses, distribution centers, and other industrial settings
- Forks and Load Capacity
- Pump Handle
- Load Rollers and Wheels
- Lowering Lever
- Compact Design
- Versatile Applications
AIR COMPRESSOR
An air compressor serves as the backbone of operations within a lube oil plant, offering essential compressed air to power an array of pneumatic tools, machinery, and vital processes throughout the facility. Its role is indispensable, supporting the seamless functioning of various operations within the plant.
At the core of its functionality, the air compressor acts as the primary source for generating compressed air, a vital utility used extensively within the plant premises. This compressed air serves as the driving force behind pneumatic tools, facilitating tasks ranging from equipment maintenance to assembly line operations with precision and efficiency.
Installed strategically within the plant, the air compressor operates tirelessly, ensuring a steady and reliable supply of compressed air to meet the diverse demands of pneumatic equipment and processes. Whether it's powering pneumatic drills, wrenches, or other tools used for maintenance activities, or providing the necessary force for pneumatic actuators in machinery and conveyors, the air compressor plays a critical role in keeping operations running smoothly.

04. AUTOMATION
PLC & MCC ELECTRICAL PANEL
The electrical panel is designed to operate all electrical motors efficiently and safely. Enclosed within a sturdy sheet steel powder-coated enclosure, it comes pre-wired for convenience. Equipped with a Motor Control Center (MCC) panel, it features a remote push button station for motor control. In case of any anomalies with the motors, the panel automatically trips to prevent damage, ensuring their safety. Premium quality switches from reputable brands such as L&T are incorporated for reliable operation. Additionally, the panel includes R-Y-B lamps, as well as digital ammeters and voltmeters for accurate monitoring of electrical parameters. Overall, this electrical control panel offers a comprehensive solution for managing motor operations in industrial settings.
The PLC (Programmable Logic Controller) & MCC (Motor Control Center) electrical panel is a comprehensive control system utilized in industrial settings to manage and regulate electrical equipment and machinery. It integrates sophisticated technology to streamline operations, enhance safety, and optimize efficiency within industrial facilities.
At the heart of the system lies the Programmable Logic Controller (PLC), a robust computing device tailored for industrial automation. The PLC serves as the central processing unit, executing pre-programmed instructions to control a wide array of electrical components seamlessly. With its programmable nature, the PLC allows for customization of logic and sequencing, enabling precise and reliable automation of complex processes.
The Motor Control Center (MCC) component of the panel acts as a centralized hub for motor management. It houses motor starters, contactors, relays, and other essential devices, facilitating the control and operation of electric motors throughout the facility. The MCC ensures efficient motor performance while providing overload protection, short-circuit protection, and fault detection capabilities to safeguard equipment and personnel.
OPERATION SEQUENCE & LOGIC Selection & Settings:
-
Selection of Storage tank & Blender for transfer done through HMI and PLC.
-
The setting of parameters like the weight of each ingredient along with the recipe management system.
-
The setting of other parameters like time specs. Etc.
Operation starts from HMI:
-
Start the operation by selecting the above parameters.
-
Respective valves & pumps will be operated in that sequence after fulfillment of required interlocks.
-
Operation sequencing will be done as per the valve status.
-
Valve, Motor and Pump status will be displayed on the HMI with Color animation
-
The current value of weight will be displayed continuously.
-
Fault & alarms will be displayed when arrives with date & time stamping. Also, it will be stored
-
Data will be logged in the HMI (Which can be used for future analysis)
-
Manual ON/OFF is also possible through HMI (Individual opening/closing of the valves)


.jpeg)

WEST AFRICA - Nigeria - LUBRICANT OIL BUSINESS GROWTH & AUTOMATION
Nigeria's is a major exporter of crude oil and petroleum products to various countries. We will delve into the country's rich oil reserves, its production capabilities, and discuss the challenges and opportunities that Nigeria faces. Nigeria's efforts to expand its industrial sector and improve its infrastructure have led to a significant increase in the demand for Lubricant Oil.
-
Exploring the Impact of Nigeria's Industrial Growth on the Demand for Lubricants.
-
The Role of Lubricants in Enhancing Efficiency in Nigeria's Automotive Industry, Manufacturing and Construction Sectors.
-
How Nigeria's Infrastructure Development is Driving the Market for Lubrication Oil.
Branch Office:
LINUS PROJECTS LIMITED (NIGERIA)
KM 15, Phase II Plaza, Jakande 1st Gate, Lekki Epe Express Way, Beside FCMB Bank, Jakande Lekki Lagos State, Nigeria, Lagos 102105, Lagos, Nigeria
LUBE OIL BLENDING PROJECTS
NIGERIA CLIENTS
Matrix Energy Group
Lagos: 4, Ademola Street, Off Awolowo Road, Ikoyi, Lagos State.
Masters Energy
21 Remi Fanni Kayode Street, G.R.A Ikeja Lagos Nigeria
Seahorse Lubricants Industries Ltd
Km 24 Onitsha - Owerri Expy, Ozubulu 435113, Anambra, Nigeria
Eraskon Nigeria Ltd
EL-AL Court, Plot 35, Chief Yesufu Abiodun Oniru Road, VI, Lagos State, Nigeria
Trustlub Fluid Resources Limited
New Makun City, Plot 2A Commercial District A, Owode 110113, Ogun State, Nigeria
Hyde Energy
3rd Floor, Canton Concourse Building, 12 Landbridge Avenue, Oniru, Victoria Island, Lagos, Nigeria
Mate Energy Industries Ltd
Km 7, Redeemed-Simawa Road, Alawun Village, Via Lotto Bus-Stop, Mowe, Ogun State
Climax Petroleum
J62W+6QX Bus Stop, Atan Kekere St, Ayobo, Lagos 102213, Lagos, Nigeria
Bucch Energy Ltd
3rd Floor, Church gate Tower 1, Plot 31 Churchgate Street Victoria Island, Lagos